Maegerle – Grinding Centres
Processes such as grinding, cutting and drilling can be achieved to absolute perfection in a single clamping. High productive benefit with simple operation are the result.
The intelligent design principle takes production quality, safety and cost efficiency to a new level.
Key Features
- Suitable for multiple-side and complete machining
- Interfaces for automated cell production with robot connection
- 24-position tool changer
- Automatic overhead dressing
- Grinding, milling, drilling and measuring in a single clamping
- Compact 5/6-axis grinding center
Available Models

Technical Specifications
X-axis longitudinal stroke | 500 mm |
---|---|
X-axis Travel Speed | 0…20000 mm/min |
Y-axis vertical stroke | 650 mm |
Y-axis Travel Speed | 0…20000 mm/min |
Z-axis transverse stroke | 650 mm |
Z-axis Travel Speed | 0…20000 mm/min |
Grinding spindle drive – power max | 25/50 kW |
Rpm range max. | 0…10000 rpm |
V-axis profile crushing device, roll width, max. | 217 mm |
Tool changer positions – grinding wheels | 8/16 n/Pos |
Tool length max | 12/24 n/Pos |
Grinding wheel dimensions (Ø-external x W x Ø-bore) | 200 mm |
Tool holding fixture HSKB-80 dividing device | 300 x 60 x 76.2 mm |
Swivel axes | 2/3 n/Axes |
Grinding wheel peripheral speed | 35 m/s |
– with key-operated switch switchable to | 50 m/s |
– with additional flange monitoring switchable up to | 63 m/s |
Form when dealing with challenging workpieces. The high axis speed, minimal auxiliary times and quick tooling change make the MFP 50 one of the most productive machines of its kind.
The intelligent design principle takes production quality, safety and cost efficiency to a new level. The coolant nozzle, controllable via two axes, allows unrestricted freedom of movement and precise positioning of the coolant jet.
Spindle speeds of up to 10 000 revolutions per minute guarantee the highest machining precision.The grinding wheels are always mounted right at the front of the spindle, and the profile is changed through automatic positioning of the diamond rolls in the direction of the Z-axis. This allows a generous machining clearance, as collisions between wheel flange and workpiece are practically excluded.
In the MFP 50 the grinding wheel diameter is used to the maximum, resulting in significant cost savings.
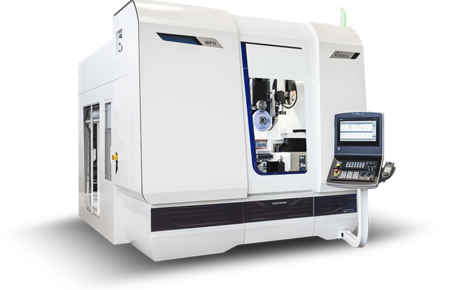
Technical Specifications
X-axis longitudinal stroke | 500 mm |
---|---|
X-axis Travel Speed | 0…50000 mm/min |
Y-axis vertical stroke | 650 mm |
Y-axis Travel Speed | 0…30000 mm/min |
Z-axis transverse stroke | 650 mm |
Z-axis Travel Speed | 0…30000 mm/min |
Maximum continuos power grinding spindle drive | 25/50 kW |
Speed range max. | 0…12000 min-1 |
V-Axis roll-in device, roll width, max. | 60 mm |
Tool changer positions | 66 n/Pos |
Nozzle changer positions | 6 n/Pos |
2 Quick release spindles | HSK-B80 |
Tool length max | 250 mm |
Grinding wheel dimensions (External x B x Bore) | 300 x 60 x 76.2 mm |
NC-Combination – Rotary-/ Swivel axis | 2/3 n/Axis |
Portal tool magazine
In its basic version this sturdy grinding center comes with an integrated tool changer in a gantry design with 66 positions. The magazine can be flexibly loaded with various grinding wheels, diamond rolls, measuring probes and tools for drilling and milling operations. The large capacity of the tool changer enables efficient machining of several different workpieces without altering the tooling.
Tool identification
An identification system for grinding wheels and tools is optionally available. The tool is inserted into a holder in the loading station. The data stored on an RFID chip is securely imported prior to the loading process. The chip is written with the current data when the grinding wheel is unloaded. The tool identification eliminates the probability of errors when entering the tool data in the machine, guaranteeing safe and uninterrupted operation.
Simultaneous tool & dresser roll changer
Very short process times are achieved with the high-speed spindle, which allows speeds of up to 12,000 rpm, and the overhead dresser integrated into the grinding support. The grinding wheels and diamond dressing rolls are simultaneously or individually exchanged with a double gripper for the individual machining steps. The compact tool holding fixtures allow an efficient grinding process and the continuously dressed grinding wheel enables high removal rates with high profile accuracy over long cuts. Additional time savings are achieved with the overhead dresser, thanks to elimination of the dressing process after the grinding cycle and the movement times to the dresser.
Process-optimised coolant supply
The 2-axis controlled coolant nozzle enables an optimal coolant supply to the tool or workpiece. Nozzles are available on the grinding support for drilling and milling tools, and a coolant supply can be provided through the spindle. The coolant supply can be ideally adapted to the process with the optionally available nozzle changer, enabling optimal grinding results.

Technical Specifications
X-axis longitudinal stroke | 1000 mm |
---|---|
X-axis Travel Speed | 0…40000 mm/min |
Y-axis vertical stroke | 900 mm |
Y-axis Travel Speed | 0…30000 mm/min |
Z-axis transverse stroke | 750 mm |
Z-axis Travel Speed | 0…30000 mm/min |
Grinding spindle drive – power max. | 50 kW |
Rpm range max. | 0…10000 min-1 |
V-axis profile crushing device, roll width, max. | 100 mm |
Tool changer positions – grinding wheels | 30/60 n/Pos |
Grinding wheel dimensions (Ø-external x W x Ø-bore) | 300 x 60 x 76.2 mm |
Tool holding fixture HSKB-80 dividing device | HSK-B80 |
Indexer swivel axes | 2/3 n/Axes |
Grinding wheel peripheral speed | 35/50/63 m/s |
Overhead dresser roll for CD / IPD / HSD | |
2 quick-clamping spindles | HSK-B80 |
integrated swivel single side dresser roll | |
Measuring system wiht feeler | |
Controll – Siemens Sinumerik 840D SL |
With the MFP 100, Mägerle AG Maschinenfabrik has expanded the MFP series with a particularly flexible grinding centre. The new grinding centre is characterised by its high working speed, quick tool change and its expandable tool changer.
Variety in one clamping operation
Mägerle has specially designed the MFP 100 for those markets where multi-face machining of heavy and complex workpieces in just a single clamping operation is demanded. With 50 kW spindle power and a generously designed working area, the new Mägerle grinding centre is ideally suited for processing turbine guide and rotor blades as well as heat shields for use in the aviation and energy industry. The Mägerle MFP 100 is supplied with a dual-axis NC combination as standard. The grinding centre can also be optionally upgraded to a tri-axis system.
Short tool change cycles
The superior tool and lapping roll changer system is an outstanding feature of the MFP 100. The dual gripper changes grinding wheels and associated diamond contour rolls simultaneously – thus resulting in a noticeable reduction in downtime. The accelerated tool change cycles are accompanied by markedly increased axis dynamics. The overall increase in productivity achieved with the new MFP 100 grinding centre results in a significant reduction in unit costs.
Up to 60 tool stations
The MFP 100 tool changer is scalable. The standard version of the tool changer can be equipped with up to 30 tool holders. It can optionally be increased to up to 60 tool stations. The MFP 100 tool management system is also generously designed and can manage up to 500 different tools. In addition to 300 mm diameter grinding wheels and corresponding 160 mm diameter diamond contour rolls, it is possible to load the tool changer with tools such as drills, milling cutters, CBN wheels or measuring sensors.
Compact and ergonomic
In spite of its performance characteristics, the MFP 100’s compact design is sure to impress. With a width of 4.6 m width and a depth of 4 m, the footprint for a grinding machine of this category is incredibly small. The NC table can be conveniently loaded from above and from the front, manually, with a crane or with a robot. The simple access opening on the rear for scheduled and preventive maintenance supports the outstanding ergonomic design of the new Mägerle grinding centre.
Key Industries
- Aerospace
- Automotive
- Defense
- Die & Mould
- Education & Academics
- Machinery & Manufacturing
- Shipbuilding
Mägerle consistently keeps the brand promise of customized grinding machines that are characterised by precision, reliability and cost effectiveness. Mägerle…
-
SINGAPORE
DKSH Singapore Pte Ltd
625 Lorong 4 Toa Payoh, #03-00
319519 Singapore
Singapore
Download now
How to Disable Pop-Up Blockers for Smooth Downloads
Google Chrome (Version 110 and later):
- Click the three dots (menu) in the top-right corner and select Settings.
- Under Privacy and Security, click Site settings.
- Scroll down to Content and click Pop-ups and redirects.
- Toggle the switch to Allowed or add https://technology-products.dksh.com.sg to the Allow list.
Mozilla Firefox (Version 90 and later):
- Click the three horizontal lines (menu) in the top-right corner and select Settings.
- Go to the Privacy & Security section.
- Scroll to Permissions and uncheck Block pop-up windows for https://technology-products.dksh.com.sg.
Microsoft Edge (Version 110 and later):
- Click the three dots (menu) in the top-right corner and select Settings.
- Scroll down to Cookies and site permissions.
- Under Site permissions, click Pop-ups and redirects.
- Toggle the switch to Allow or add https://technology-products.dksh.com.sg to the Allow list.
Safari (Version 14 and later):
- Open Safari and go to Preferences (from the top menu).
- Select the Websites tab.
- Under Pop-up Windows, select Allow for https://technology-products.dksh.com.sg.